- May 11, 2008
- 22,283
- 1,425
- 126
As mentioned in the PM435 lcd thread, i am helping out a friend with his bench supply. I do this in parallel with the creation and design of my own bench supply.
He wants a beefier old fashion power supply. 2x0 to 30V@5A. So, 30V @ 10A.
He bought a toroidal transformer of 230V AC primary and 2 secondary coils of 35V rms @6.44A. We are going to put these secondary coils in parallel.
Example picture of a toroidal transformer :
Unfortunately, the electronics can stand up about 40V absolute maximum and when the secondary rms voltage is unloaded, it will climb up to about 37V. Rectified, this would mean 52.17V (37 * 1.41). A bit to much. So i have the fun task of unwinding the transformer. I want a peak DC voltage (after rectifying) of about 37V DC so i am planning to unwind the coils to about 27V rms AC. To see if this is sufficient to get 33V@ 10A, i do have to put a load on the secondary coils and test if it will be sufficient. Otherwise, i have to solve that issue by changing the specs of the power supply. Or just use an electronic schematic that can handle the high voltage. Normally i would have already done this. But unfortunately my friend already bought the components, so this is what i have to work with for now.
I also need another auxiliary winding of about 12V @ 200mA to create a 9V stabilized supply for the PM435 lcd panel meters. Doing only this would have been easy with a toriodal transformer. Just wind a few meters of insulated copperwire and have myself an auxiliary coil. And that is what i am going to do.
As it is now, before modification, to create one secondary coil, 2 windings are put in parallel. Each winding consists of 1.35mm2 insulated copper wire. The insulation is very thin, so i have to be careful here not to damage it.
I was hoping to unwind the two wires in parallel. But unfortunately the secondary stage of the transformer consists of 4 coils layed over each other.
So, i have to unwind 3 coils entirely and one coil until i have the voltage i need. :|
The thought of having the voltage i need and delayed gratification keeps me going here.
I will post pictures later on.
He wants a beefier old fashion power supply. 2x0 to 30V@5A. So, 30V @ 10A.
He bought a toroidal transformer of 230V AC primary and 2 secondary coils of 35V rms @6.44A. We are going to put these secondary coils in parallel.
Example picture of a toroidal transformer :
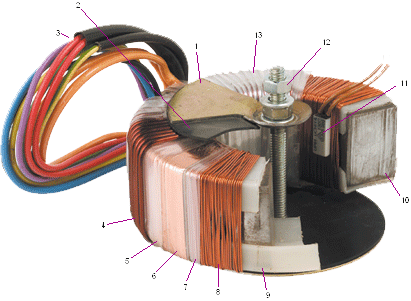
Unfortunately, the electronics can stand up about 40V absolute maximum and when the secondary rms voltage is unloaded, it will climb up to about 37V. Rectified, this would mean 52.17V (37 * 1.41). A bit to much. So i have the fun task of unwinding the transformer. I want a peak DC voltage (after rectifying) of about 37V DC so i am planning to unwind the coils to about 27V rms AC. To see if this is sufficient to get 33V@ 10A, i do have to put a load on the secondary coils and test if it will be sufficient. Otherwise, i have to solve that issue by changing the specs of the power supply. Or just use an electronic schematic that can handle the high voltage. Normally i would have already done this. But unfortunately my friend already bought the components, so this is what i have to work with for now.
I also need another auxiliary winding of about 12V @ 200mA to create a 9V stabilized supply for the PM435 lcd panel meters. Doing only this would have been easy with a toriodal transformer. Just wind a few meters of insulated copperwire and have myself an auxiliary coil. And that is what i am going to do.
As it is now, before modification, to create one secondary coil, 2 windings are put in parallel. Each winding consists of 1.35mm2 insulated copper wire. The insulation is very thin, so i have to be careful here not to damage it.
I was hoping to unwind the two wires in parallel. But unfortunately the secondary stage of the transformer consists of 4 coils layed over each other.
So, i have to unwind 3 coils entirely and one coil until i have the voltage i need. :|
The thought of having the voltage i need and delayed gratification keeps me going here.
I will post pictures later on.
Last edited: