- Jun 30, 2004
- 16,118
- 1,730
- 126
I continue, little by little, to pursue my "modernization" plan for my '95 Trooper.
The MP3 player I added -- explained in a thread that's slowly going stale (but it had 1K views!) -- required a piggy-back fuse-tap. It overhangs another fuse, related to my Anti-Theft System, which is also on the schedule to resurrect and repair. I'll probably post a thread about that project -- later. It was a "mystery solved" as I remember some things I did back in September 2018, when my rear window was shattered and then fixed. Interesting story, but -- for later.
Even so, to resurrect the Anti-Theft system, add an interior LED lighting system and a backup camera, I figured it was time to scrap this "fuse-tap" nonsense -- at least, almost.
So I decided to add a "fuse box extension". These things are pretty simple. Some are bulky. Some have little LED lights to warn that a fuse is blown. Some have screw terminals. Some have a construction that offers several of the load connections connected together.
Here's the one I bought:
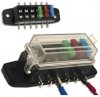
I took a 12-inch length of 14-guage wire, and soldered a brass fuse-tap to it. The tap will go on the load side of the ACC/accessory bank of fuses. The other end of the wire is soldered to six female spade connectors. Once the spade connectors are attached to the fuse-box extension shown here, they widen the assembly by maybe 1.5 inches. Of course, the connections are all solid.
After looking for a place near the OEM fuse-box to install this extension, I settled on a metal panel just below the OEM item. I'll probably use a patch of Flex-Seal tape to secure it to the panel, and I don't think it will just come off some time later very easily. That stuff is f***ing sticky! There's little way I can drill holes for sheet-metal screws and use that method, so the adhesive tape is the next best thing.
But there's still not a great deal of room for the assembly. And I'm thinking I'd like to just solder my blue 14-gauge wire across all the load side male spades. Of course, there's the risk of damage to the plastic extension box from the heat conducted from the solder gun.
But I have a table-top clamp or vise, and I've discovered that I can take a pair of needle-nose pliers, clamp the desired item to solder, hold the pliers tight and clamp them in the heavy vise. The needle-nose pliers then act as a heat-sink.
Once I have good soldered connections across the spades or blades, I can then just coat the wire and the blades with silicon adhesive/sealant. I can even wrap it all in self-adhesive rubber hose-bandage or repair tape, and it should all be well-insulated.
Anyone with a lot of soldering experience want to comment on my plan here, before I sit down and actually do it?
The MP3 player I added -- explained in a thread that's slowly going stale (but it had 1K views!) -- required a piggy-back fuse-tap. It overhangs another fuse, related to my Anti-Theft System, which is also on the schedule to resurrect and repair. I'll probably post a thread about that project -- later. It was a "mystery solved" as I remember some things I did back in September 2018, when my rear window was shattered and then fixed. Interesting story, but -- for later.
Even so, to resurrect the Anti-Theft system, add an interior LED lighting system and a backup camera, I figured it was time to scrap this "fuse-tap" nonsense -- at least, almost.
So I decided to add a "fuse box extension". These things are pretty simple. Some are bulky. Some have little LED lights to warn that a fuse is blown. Some have screw terminals. Some have a construction that offers several of the load connections connected together.
Here's the one I bought:
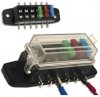
I took a 12-inch length of 14-guage wire, and soldered a brass fuse-tap to it. The tap will go on the load side of the ACC/accessory bank of fuses. The other end of the wire is soldered to six female spade connectors. Once the spade connectors are attached to the fuse-box extension shown here, they widen the assembly by maybe 1.5 inches. Of course, the connections are all solid.
After looking for a place near the OEM fuse-box to install this extension, I settled on a metal panel just below the OEM item. I'll probably use a patch of Flex-Seal tape to secure it to the panel, and I don't think it will just come off some time later very easily. That stuff is f***ing sticky! There's little way I can drill holes for sheet-metal screws and use that method, so the adhesive tape is the next best thing.
But there's still not a great deal of room for the assembly. And I'm thinking I'd like to just solder my blue 14-gauge wire across all the load side male spades. Of course, there's the risk of damage to the plastic extension box from the heat conducted from the solder gun.
But I have a table-top clamp or vise, and I've discovered that I can take a pair of needle-nose pliers, clamp the desired item to solder, hold the pliers tight and clamp them in the heavy vise. The needle-nose pliers then act as a heat-sink.
Once I have good soldered connections across the spades or blades, I can then just coat the wire and the blades with silicon adhesive/sealant. I can even wrap it all in self-adhesive rubber hose-bandage or repair tape, and it should all be well-insulated.
Anyone with a lot of soldering experience want to comment on my plan here, before I sit down and actually do it?
Last edited: